线在包装以下行业(产线包装产业)
运用于包装产业之运动控制技术
在传统产线包装应用,先进控制功能与伺服马达取代步进马达为”未来合乎逻辑的优势”,
图一,传统产线包装应用
有许多产线包装应用,包含贴标机,定尺寸切割,飞剪,追剪,分条,刀具旋转等许多商业应用。这些产线应用都有相同机器功能程式。这些机台中有一个很大的共通点,也就是他们通常地会有一个独立移动线量测线速度做回馈。这个回授讯号输入透过辅助编码器输入到运动控制器。然后运动控制器使用辅助编码器输入如控制命令,当它控制其他次轴或追随轴移动到相同的速度。线速度与追随速度可以为一比一比例或“其他功能或比例”。
在产线上,除了需要同步上线速度,指定点(或位置)必须同步于追随轴。在产线上,为了标记位置,透过装置的高速输入接点,使用感测器量测物件的位置,(如“光遮断器,测重平台等”)。此时,产线的位置就会被截取下来。
若已知标记位置与距离(感测器器与轴控距离),控制器计算一组轨迹,为了吻合追随轴的位置与产线的位置。产线上追随轴的位置轨迹。简单的说,控制器必须配合轴的速度与位置。它正在控制一条独立产线基于速度与事件感测器。
产业需求
一般多数产线机器使用步进马达。但当他们需要精密的控制,需要更有高解析度,更聪明,与有能力下载资料,更好的人机介面,与更多的装置故障讯息时,伺服马达就会变的重要。此外,软体明显的差异与控制方式,让机器制造商使用不同的部件用于机器的各个部份,部分区块使用步进马达,其他区块使用伺服马达来进行运动。
包装机加工速度为成本与产能的主要关键例如:在贴标机的应用,传统精度为1/32英寸(0.79375毫米),与产线速度为2000〜3000英寸/分(50,800〜76200毫米/分钟)。这代表控制包装流程将会需要高速IO与全功能运动轨迹。另外,一些旧的机器内包含一PLC装置与一个运动驱动器。当升级新软体与硬体时,这增加复杂性与工时。
艾特航空在包装产业的优点与好处
![]()
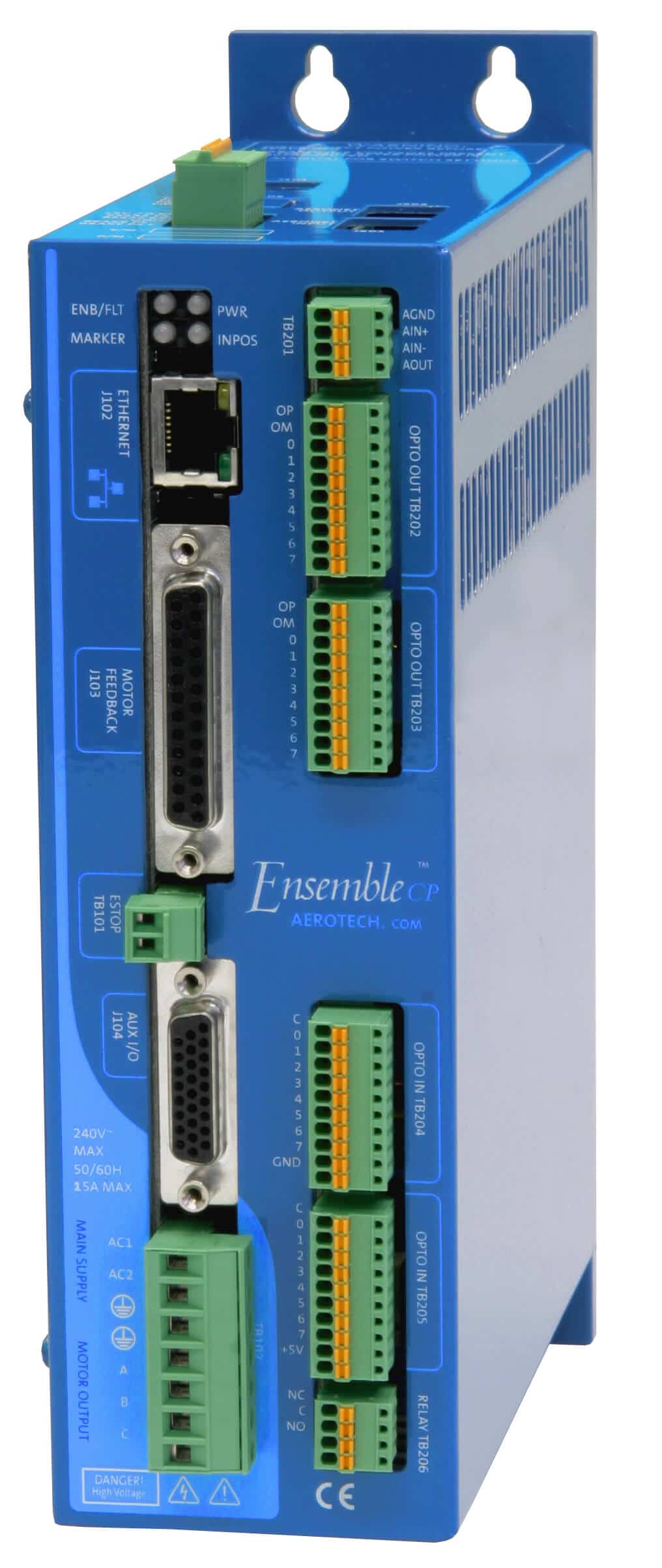
图二:艾特航空的合奏CP
艾特航空针对包装产业,提供强大软体功能与灵活性高的驱动器与马达。使用这些产品编写复杂的程式的能力,使其成为今日苛刻应用的良好选择。
多种类马达驱动技术:艾特驱动产品能在不改变软体与硬体的情况下,驱动步进马达与伺服马达。这代表在同一个平台上,只需改变参数后,一个驱动器就能控制步进马达与伺服马达。此外,使用相同的硬体与软体的优势代表着从步进马达切换到伺服马达的成本降低。
高速IO:的Aerotech驱动器提供高速IO。包含双组高速输入与输出。驱动器还能基于许多不同的输入讯号,计算全功能的同步运动轨迹,将其用在带动快速和复杂的制程。驱动器有两组高速输入接点与一组50奈秒延迟时间接点。高速输出,PSO讯号,为一组可程式化单轴同步位置触发,延迟时间为160奈秒。
辅助编码器:艾特驱动器包含一组辅助编码器输入。这组辅助编码能被使用在高精度应用的双回路控制,输出主要编码器讯号到外部装置,或在产线应用,将外部编码器讯号接进驱动器当作追踪目的。这组输入接点能接受的10MHz的四倍频A,B相讯号
PLC到运动控制:艾特航空产品可当作PLC与运动控制器元件,用来降低复杂性,减少程式编辑与整合成本,且增加每个元件的功能性
数据处理:艾特驱动器透过工业乙太网通讯协定(以太网/ IP™),提供与RFID阅读器连接,储存资料到网路与回应即时讯息的功能。
工业乙太网通协定(以太网/ IP™):艾特驱动器支援工业工业乙太网通协定汇流排。这允许运动控制器直接透过Allen Bradley的协定沟通与被的RSLogix程式控制。
全面性整合:艾特航空.NET函式库能被整合到视觉系统中。通过先进运动功能,将视觉与运动同步。
客制化控制:艾特航空为垂直整合供应链的公司,且艾特航空工程部涉及广泛的工程学科。这让可以对软硬体每个部份进行客制化以适用到应用中的确切需求。范例包含OEM驱动器包装,客制化软体与函式库与客制化马达设计。
程式编辑概念
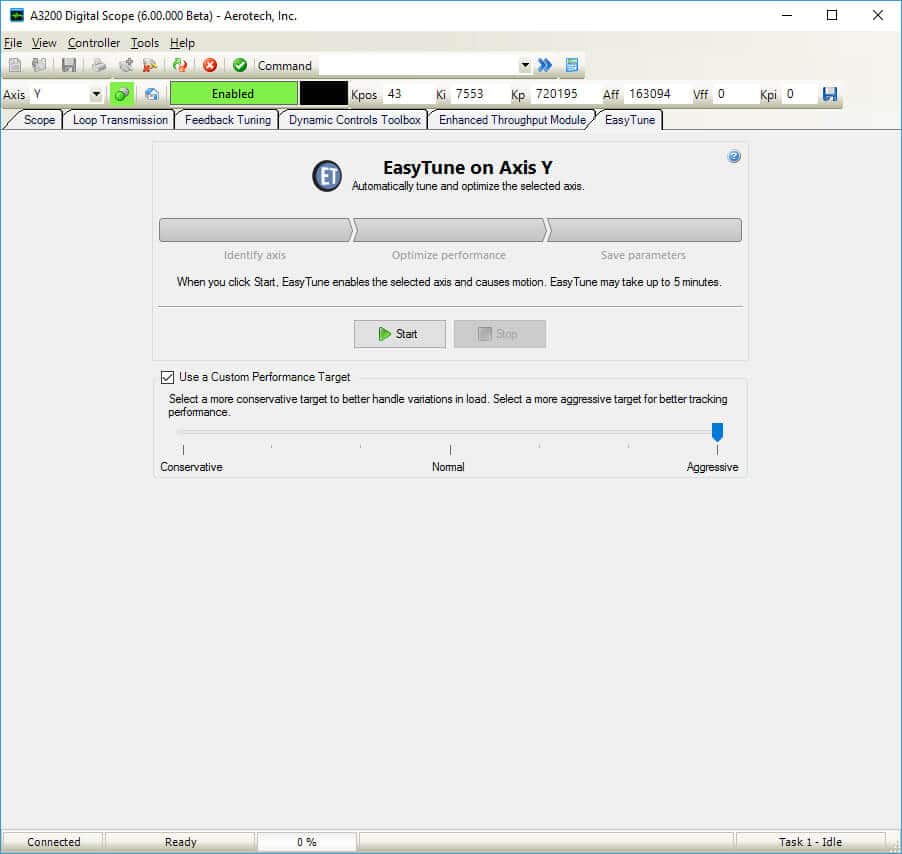
图三,合奏任务计算器
的Aerotech控制器包含多个任务(任务)。这些任务可以被使用在确保多组产品能被标记在一组线与运动发生分开。在下面范例,我们在合奏控制器上使用两个任务任务。一被使用在运动轨迹与任务三使用在标记输入。我们使用IGLOBAL暂存器将讯息传递在两个任务间。
合奏任务计算器使用在帮任务分配周期时间。这里有五个任务片段(任务切片),任务1到任务4使用4个任务片段。第五个任务包含各种流程,每一毫秒一次,其中一个为辅助任务。
我们需要设定多组任务用来执行多组程式。任务一与任务三使用相同的时间片段,这个允许每个任务有100微秒时间片段。可以选择从不同的任务间,给予一个任务有较高优先权,下面展示程式给任务有相同的优先权执行
下面程式码展出一套贴标机在瓶罐上应用所需的步骤。光电感测器接到合奏CP驱动器的高速输入接点。这个输入点在硬体层由POSCAP功能使用.POSCAP功能使用在标记皮带的位置。从输入讯号被触发到这个位置被撷取,含有400奈秒(纳秒)延迟时间。
已知从光电感测器(或称为电眼照片眼)到标签的固定距离。使用POSCAP功能纪录数值,程式将准确地知道什么时候转动马达放置标签在瓶罐上。
图4.瓶贴标签应用与光眼。
图四,贴瓶机搭配光电感测器(电眼)的应用
图五,五个部件被触发
上图里五个部件被触发。位置撷取位元(位置捕获位)= 0,此时被触发。当瞄准时,位置撷取位元= 1。如图可见触发讯号彼此间有不同距离。在第一组标签到达之前,我们能有多组触发。这是好方式,程式将持续纪录所有触发数值与在部件使彼此间维持正确距离,只要运动能在下一个部件进入视窗之前完成执行。这应用时间将成为皮带移动速度能有多快的一个限制因素,或皮带上的原件能有多近。
我们撷取从上到下顺序,位置回馈,速度命令,位置撷取位元(合奏中的状态),数位输入接点正被位置撷取位元,与皮带上编码器
因为AERONET运动汇流排有非常高判断,我能“拨入”我们的移动位置。为了轴的延迟时间,在运动程式里EyeToLabelDistanceInCounts变数能拥有一个偏移量到“帐号”
这个延迟在程式里会有一个固定数值,且同常为3-5ms决定于哪种位移命令被使用。我们能够简单地使用这个延迟时间去计算它的线速度。这将完全自动化”线”所以终端使用者能调整速度,不用重新调整标签位置。
下页显示放大后的测试结果。
触发1显示显示撷取触发位置与轴运动间之距离为123750个计数
图六
图七
触发2显示撷取触发位置与轴运动间之距离为123749个计数。
图8。
图9。
图九
触发3显示撷取触发位置与轴运动间之距离为123759个计数
图十
图十一
触发4显示撷取触发位置与轴运动间之距离为123751个计数
图十二
图十三
触发5显示撷取触发位置与轴运动间之距离为123,746counts
图十四
图十五
在这个范例,每英吋有50800个计数进入辅助编码器输入。皮带曾移动在42英吋/秒或2520 IPM。最坏情况下,触发机制被使用在追踪与启动运动中有751个计数。从目标位置到每个不同触发点之间不差于4个计数。
我们是否曾透过反覆测试将触发延迟降到0但即使不用这个方式,结果也是非常精确。这系统测试能在速度2520 IPM下,能精确地放置一个标签在0.015英吋,约67分之1英吋(0.379毫米)且有0.0001英吋的重覆精度。